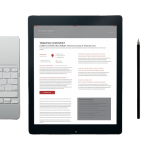
Una de las necesidades imprescindibles de las industrias es el análisis de fallos en mantenimiento. Los errores en equipos y maquinaria pueden dar lugar a un largo tiempo de inactividad, lo que supone importantes riesgos para la producción.
Entender por qué se producen los fallos en un sistema o proceso es, por tanto, determinante para mejorar la eficiencia de la industria, y una de las claves para desarrollar un plan de mantenimiento preventivo que ayude a optimizar los costes.
A continuación vamos a tratar de explicarte qué es el análisis de fallos y su importancia en el plan de mantenimiento de una empresa, así como los diferentes métodos que existen para poder aplicarlo en tu negocio.
¿En qué consiste el análisis de fallos en mantenimiento?
Se trata de una técnica de mantenimiento orientada a descubrir las causas por las que se producen las averías o fallos en las máquinas, equipos, sistemas o procesos de una industria.
Este tipo de enfoque, basado en el mantenimiento productivo total, busca como principal prioridad acudir a la raíz de cada fallo para corregir las causas desde su origen y tratar de evitar así futuros problemas. En este sentido, aplicar el análisis de fallos permite adquirir un conocimiento acumulado que mejora la eficiencia de los procesos en la industria.
Métodos utilizados en el análisis de fallos en mantenimiento
Existen diferentes metodologías que las empresas pueden aplicar para adaptarse a una estrategia de mantenimiento 4.0, que aproveche el potencial de los datos para actuar antes de que los problemas se produzcan.
Análisis de causa raíz (RCA)
El análisis de causa raíz, también conocido como Root Cause Analysis por sus siglas en inglés, trata de abordar las causas principales de un problema en un sistema, y no limitarse sólo a los fallos más visibles.
Este enfoque basa su estrategia en la inspección e identificación de posibles conflictos a partir de toda la información de valor disponible. Para ello, se exploran las causas más inmediatas y se trabaja hacia atrás para determinar cuál es la raíz del incidente y visualizarla claramente, de manera que se pueda llegar a la solución más idónea.
Diagrama de Ishikawa
El objetivo de los diagramas de Ishikawa es entender la raíz de las deficiencias que se producen en el sistema. Creado originalmente por Kaoru Ishikawa, esta metodología pretende detectar errores a través de una representación gráfica que permita entender las relaciones causa-efecto de todos los problemas asociados al incidente.
Denominado también como diagrama de espina de pescado, requiere identificar los elementos perjudiciales persistentes en un sistema, proceso o fallo técnico para poder solucionarlo.
Concretamente, las partes principales del diagrama se conocen como a) cabeza o espina central; b), las espinas grandes (que son las líneas que parten de la espina central); y c), las espinas menores (que se derivan de las espinas grandes). Este diagrama permite así analizar la interacción de las distintas partes de los sistemas y las diferentes aristas que pueden estar involucradas, desde los materiales a la maquinaria o la mano de obra.
Análisis de modos de fallo y efectos (AMFE)
El análisis de modos de fallo y efectos (AMFE) es un enfoque orientado a anticipar los posibles problemas e identificar los fallos que se producirían en un sistema, producto o proceso, y llevar a cabo un análisis de las consecuencias que podrían producirse. Esta metodología permite aprovechar así todas las ventajas del mantenimiento predictivo.
Entender los modos de fallo en mantenimiento es clave para reducir los costes y mejorar la calidad, ya que se busca anticipar los fallos. Para ello, se identifican posibles riesgos, se lleva a cabo una priorización de los riesgos según una puntuación numérica de acuerdo con su importancia y a continuación se implementan acciones correctivas para reducir la probabilidad de que se produzcan o disminuir sus posibles efectos.
Análisis de árbol de fallos (AAF)
El análisis de árbol de fallos (AAF) es una metodología de gran utilidad para evaluar riesgos en sistemas complejos. Consiste en dividir un fallo principal en pequeñas causas simples, utilizando para ello como modelo un diagrama de árbol invertido.
De este modo, se pueden determinar las rutas que conducen al fallo de mantenimiento, evaluar la probabilidad de que se produzcan y establecer las medidas preventivas adecuadas.
¿Por qué es importante hacer un análisis de fallos en mantenimiento?
El objetivo del análisis de fallos es adquirir conocimiento sobre los fallos técnicos que se producen para poder aplicar medidas que eviten que se vuelvan a producir en el futuro. Hay que tener en cuenta que los errores en las máquinas, sistemas, equipos o procesos pueden dar lugar a una pérdida de rentabilidad, debido al tiempo de inactividad que se ha producido hasta que se ha logrado encontrar la forma de solucionar el fallo.
Aplicar técnicas de análisis de fallos te permitirá reducir los costes futuros y mejorar así la rentabilidad de tu negocio, así como salvaguardar la seguridad de tu personal, en el caso de que dichos fallos puedan convertirse en accidentes que afecten a tu equipo.
Pasos para realizar un análisis de fallos en mantenimiento
Todo análisis de fallos de mantenimiento implica seguir una hoja de ruta para obtener los datos, evaluar los riesgos y el impacto de los fallos, revisar los procedimientos implicados y aplicar las medidas correctivas.
Veamos punto por punto cada etapa del proceso.
Recopilar toda la información relevante sobre el fallo
La primera etapa de un análisis de mantenimiento es reunir todos los datos relacionados con la incidencia para poder entender su contexto.
Realizar una investigación de causas raíz
A partir de los datos acumulados, el siguiente paso consistirá en realizar las acciones oportunas para identificar los factores que dieron lugar al fallo, utilizando para ello los métodos de análisis de fallo de mantenimiento que antes se han mencionado.
Evaluar el impacto del fallo
Otro aspecto capital que hay que tener en cuenta en el análisis de fallos es el análisis de las consecuencias de la incidencia a todos los niveles. Por ejemplo, en qué medida ha contribuido a aumentar los costes de producción, o cuál ha sido el tiempo de inactividad generado, o los riesgos para la seguridad del personal, o en qué medida ha afectado a otros procesos. Todo esto se debe cuantificar y medir de la manera más precisa posible.
Revisar procedimientos de mantenimiento preventivo
Una vez se han identificado las causas, hay que revisar los procesos de mantenimiento preventivo y analizar cuáles son las prácticas que se llevan a cabo habitualmente y modificarlas para tener en cuenta la incidencia que se ha producido. De este modo, se podrá evitar que dicho evento se vuelva recurrente.
Tomar medidas correctivas
Por último, es clave Implementar las soluciones más efectivas para corregir las causas que se han identificado anteriormente y minimizar los riesgos futuros.
¿Qué herramientas se utilizan para el análisis de fallos en mantenimiento?
Nuestro consejo es que para llevar a cabo tu estrategia de mantenimiento preventivo en tu industria empieces por una digitalización eficaz a través de un programa ERP de mantenimiento.
Este tipo de solución te permite establecer las bases de tu estrategia de mantenimiento predictivo, preventivo y correctivo de manera sistemática y organizada, con fechas programadas de mantenimiento y análisis de datos que te permitirán aprovechar el conocimiento acumulado de las tareas realizadas para mejorar la eficiencia y hacer que las tareas de mantenimiento en tu empresa sean más precisas y efectivas.